Batik Through The Globe: Indonesia
- Lekasiny Sivakumar
- Nov 19, 2020
- 5 min read
Updated: Nov 26, 2020
In Indonesia, batik is more than just fabric; It is regarded as an art form and a way of life. The word batik is derived from the word “ambatik” which means “a cloth with little dots”. However, there is a more romantic phrase; the Javanese created for the mystical experience of making batik. “Mbatik Manah”, which when directly translated means “drawing a design on the heart”.
Indonesian’s treat batik as a traditional art that is to be revered and respected. Therefore, even the selection process in regards to the material used to make batik is highly intricate. Natural materials like cotton and silk are used as the cloth, as they are highly absorbent. This enables the wax to be absorbed sufficiently for the dye resisting process. The fabrics used must posses a high thread count to ensure the intricate design quality of the batik is maintained. The cloth is then washed and boiled numerous times prior to the wax application process to ensure that the traces of starch, chalk, lime and other sizing materials are completely removed. In the older days, the cloth was pounded with a wooden mallet and then ironed to create a smooth and supple texture. However, in the modern world we have replaced this painstaking process with machine made cotton. Therefore, the process of pounding can be omitted. As time passed the industry standard changed, today there are levels to the quality of the material used which is Primissima (the best quality) and Prima. The cloth quality is often mentioned in writing at the edge of every design.
Batik Design Tools
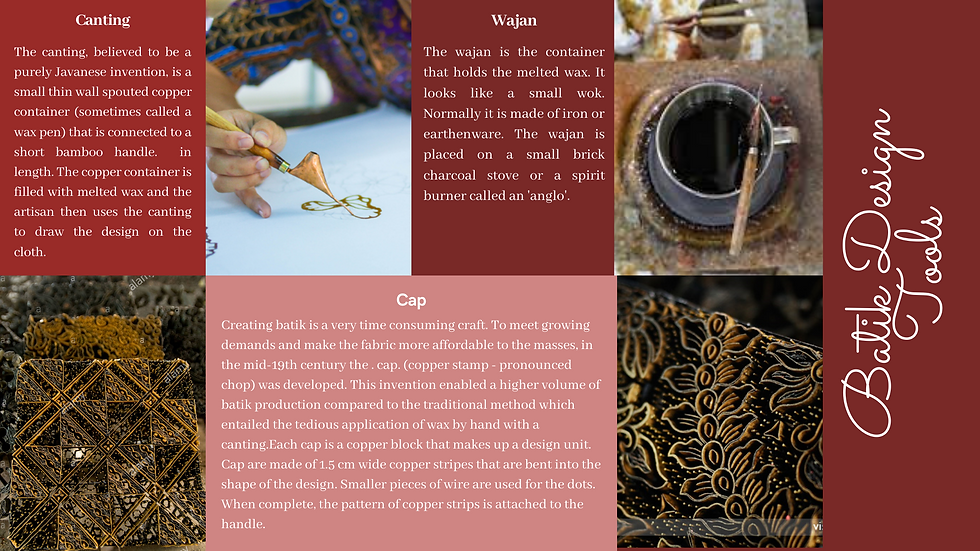
Batik Dye Color Scheme

Batik Design Process
The design process of Indonesian batik is extremely intricate. They begin by creating the outline of the pattern that is onto the cloth. Traditionally charcoal or graphite is used for this part of the process. In the case of traditional batik designers, they often utilize the patterns that have been handed down over the generations. Those designs are rich with culture and history. The skill of an artisan is no match to the intricacy of batik, as it is very seldom that they are able to draw from memory. Most artisans draw the outline of the pattern prior to applying the wax. Often designs are lifted off stencils or patterns called "pola". The other method in which the pattern can be drawn is by tracing it. This process requires the cloth to be laid on a glass table that is illuminated from underneath. This casts a shadow of the pattern onto the cloth, and the pattern is traced with a pencil. Once this process is completed the waxing and dyeing process begins.
Batik Waxing Process
Upon the completion of the design process, the cloth is then ready to be waxed. The wax is then applied to the cloth to maintain the original color (white or cream), this is to maintain the desired look the artisan wishes to achieve. Female workers are often found bent over a low stool or a mat to apply the wax with the canting tool. The fabric is laid across light bamboo frames called "gawangan" to make sure the freshly applied wax cools and hardens. The process of heating the wax takes places on the "wajan" until a perfect consistency is achieved. The artisan then dips her canting into the wax to fill the bowl of the canting and begins to retrace the pencil outline on the fabric.
The Artisan of Batik Nglengreng

The true process of Batik begins at the hands of the artisan; bent over her stool she keeps a small drop cloth on her lap to protect her from the hot dripping wax. The stem of the canting is held with her right hand horizontally to ensure there is no accidental spillage, as an accident like that will greatly reduce the value of her hard work. She uses her left hand to support the fabric from the back. The spout never touches the fabric, but is held slightly above the area the artisan is working on. To create the perfect well defined batik, it is waxed on both sides. However, true batik "tulis" is reversible as the pattern needs to be identical on both sides.
An artisan of true merit begins their batik journey with the first waxing. While filling in large areas may be entrusted to less experienced artisans the mistakes made are extremely difficult to correct. In the event the was accidentally spills on the cloth the artisan will try to remove the unwanted wax by sponging it with hot water. Then they use a heated iron rod with a curved end to lift off the remaining wax. Spilled wax much like spilled ink can never be completely removed; which is why it is important that the artisans pay special care to this part of the process.
The Process of Batik Ngecap

Photo By: Dewi Sundari
"Ngecap" is a process that refers to produce Batik patterns on a piece of linen cloth by using a bronze stamp filled with hot-melted wax. The cap method however is normally done by men. The cap is dipped into melted wax and just under the surface of the melted cloth is a folded cloth approximately of 30cm square. This cloth needs to be saturated with wax so that it can act as a stamp pad. The cap is pressed onto the fabric until the designs of the cap is coated with wax. The saturated cap is then stamped onto the fabric, the beautiful design of the cap will be left behind on the fabric. This process is painstakingly repeated until the entire cloth is covered. Often artisans combine the cap and the canting method to give each piece of batik the best of both worlds.
Batik Nyelup Process
"Nyelup" refers to the soaking process of the Batik textile in a barrel filled with natural/chemical dye solutions. After the waxing process is complete, the fabric is prepared for its first dye bath. Traditionally, dyeing is done in earthenware tubs and above the vats are ropes with pulleys that the fabric is draped over after it has been dipped in the dye bath. The first dip is the first color the batik will receive. The longer the batik cloth is left in the bath the darker the color will be. Once it has been dipped into the first color it will be then put into cold water to harden the wax.
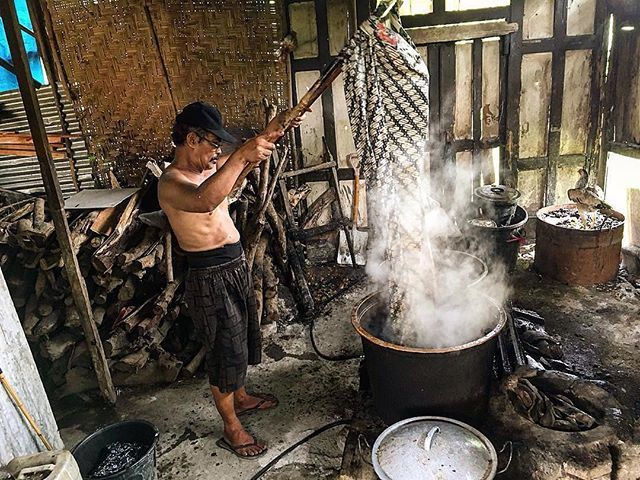
Photo By: Jo Souvenir
When the color desired by the artisan has been achieved and the fabric has dried, wax is reapplied to the areas where the artisan wishes to maintain the first dye color or a second color at the later stage in the dyeing process. If the artisan wishes to add a new color, the area that has been covered with wax before needs to be exposed and the applied wax needs to be removed with a small knife. The area is then sponged off with hot water and resized using rice starch before it is re-immersed in the next dye bath.

Photo By: Elisa Quevedo
If the artisan desires a marble effect, they intentionally crack the wax before placing it into the dye bath. The dye then seeps into the hairline cracks in the wax and creates the fine lines typically seen in batik. Traditionally however these fine lines were an indicator of inferior cloth especially when it is seen on indigo colored batik. The exception to this rule is marbling on brown batik.
The variations of colors in batik represents how many times it was immersed in the dye bath and how many times the painstaking process of reapplying and removing the wax occurred.
A multicolored batik represent more time and effort in comparison to batik that has a single color or dual colors. The price of the batik material is also determined by the colors on the batik.
Batik Designs

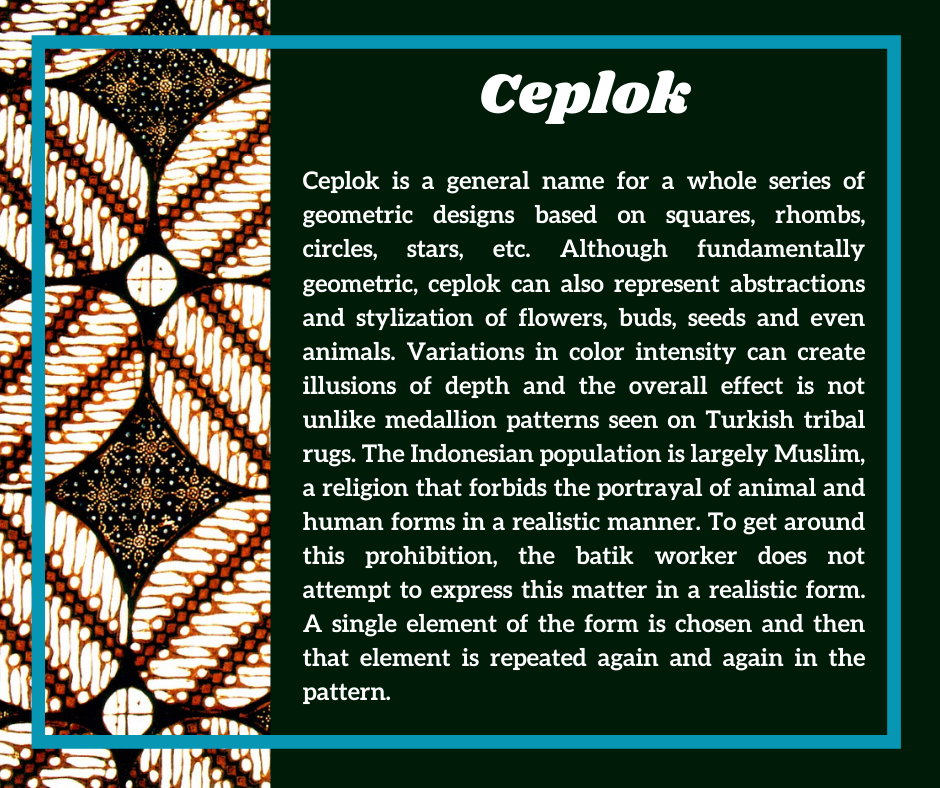

Comentarios